Managing Efficiently Bill of Materials to Produce a Product
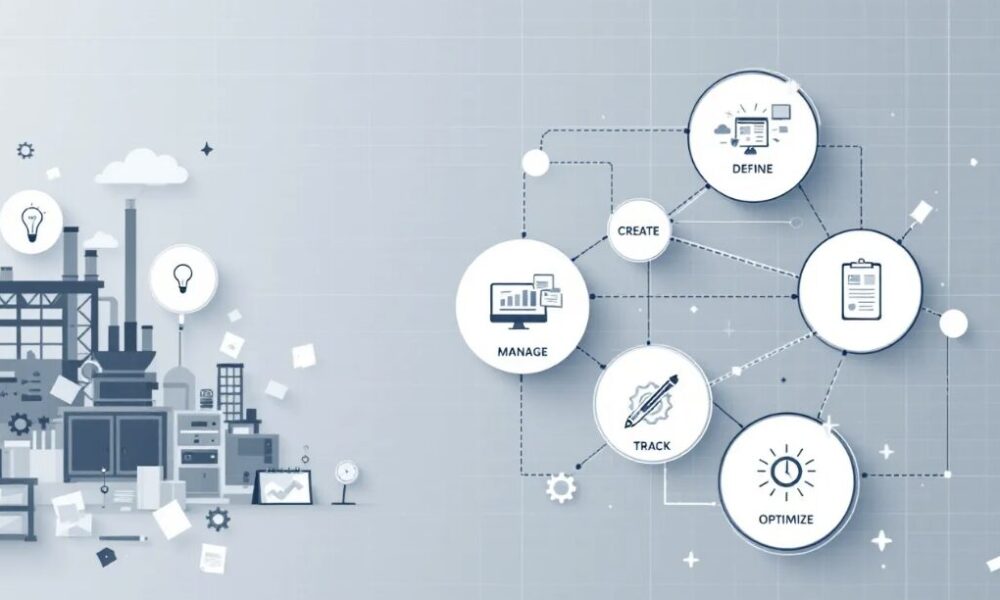
The Bill of Materials (BOM) management system is a crucial software tool that streamlines the manufacturing process by efficiently managing all the materials, parts, and components required for product development. This system organizes and integrates the key aspects of production planning, material quantities, suppliers, and inventory, helping manufacturers meet customer requirements while maintaining a reasonable cost of production.
A Bill of Materials essentially provides a detailed breakdown of all the materials and components needed to manufacture a product. It specifies the quantity of each item, the sequence of steps to assemble the parts, and any other critical details required for producing the product. By managing these details effectively, manufacturers can improve the efficiency of the production process, even when the complexity of the product increases. Whether producing simple consumer goods or intricate machinery, a BOM ensures that every part is accounted for, and the process remains streamlined.
For example, when producing a laptop, the BOM will list all the required components, such as the processor, keyboard, monitor, casing, and keys. These are all essential raw materials that come together to form the final product. The BOM system also provides access to engineering drawings, which show detailed plans of each part and component needed. It allows manufacturers to plan and track each part’s role in the final assembly, ensuring nothing is overlooked.
The BOM management system is typically divided into two key categories: the Engineering Bill of Materials (EBOM) and the Manufacturing Bill of Materials (MBOM). Each serves a specific purpose and plays a vital role in the overall production process.
Engineering Bill of Materials (EBOM)
EBOM focuses on the design aspect of the product. It is a specialized list that contains all the components, parts, assemblies, subassemblies, and other items that the engineers designed for the product. This type of BOM ensures that the product is made according to the design specifications, outlining how the individual parts and components will fit together. It is essentially a blueprint for the product’s design and acts as the foundation for the manufacturing process.
Manufacturing Bill of Materials (MBOM)
MBOM, on the other hand, is more focused on the practicalities of production. It includes all the assemblies and parts needed to build the product, and it takes the design specifications from the EBOM and translates them into a set of actionable steps for the production team. The MBOM also includes a “Bill of Process” (BOP), which details the workflow and step-by-step instructions on how to assemble the parts. The BOP guides the manufacturing team, ensuring that each part is put together in the correct order and manner.
One of the most complex tasks in BOM management is starting the Bill of Process. This involves managing a large amount of data and ensuring that the most up-to-date versions of all the components are used. Inaccurate or outdated information can lead to production delays, errors in assembly, or issues with the final product quality.
Material Considerations
Material selection plays a crucial role in the efficiency and quality of the final product. It is important to choose materials that meet the customer’s requirements and specifications, while also considering the cost implications. For instance, branded or premium-quality materials may come at a higher cost, but they might be necessary for achieving the desired performance or durability of the product. However, manufacturers should carefully balance cost with quality to avoid sacrificing product integrity for the sake of cheaper components.
Choosing the right materials also requires continuous monitoring. By maintaining quality control over the raw materials, manufacturers can ensure that the final product meets the necessary standards and performs well in the market. Failure to properly monitor material quality can lead to defects, poor product performance, or customer dissatisfaction, which can ultimately damage a brand’s reputation.
Benefits of BOM Management
A well-managed BOM system brings multiple benefits to manufacturers. It significantly improves inventory management by allowing for better tracking of materials, components, and subassemblies. This minimizes waste, reduces the risk of stockouts, and ensures that production flows smoothly without unnecessary delays. The increased collaboration between engineering teams and manufacturers is another key advantage, as it fosters better communication and ensures that everyone involved is on the same page.
Furthermore, BOM management helps reduce production costs. By clearly outlining all the materials and processes needed, it allows manufacturers to better estimate costs and avoid overproduction or shortages. Accurate cost estimations are essential for pricing products competitively while maintaining healthy profit margins. In addition, BOM systems support the Product Lifecycle Management (PLM) system, which tracks the product through every stage of its lifecycle, from design to disposal.
Lastly, the success of manufacturers, regardless of their size or the complexity of the products they produce, is heavily influenced by how effectively they manage their Bill of Materials. A well-structured BOM system ensures that production runs smoothly, quality is maintained, and costs are kept under control. In industries ranging from electronics to automotive manufacturing, the efficient management of materials is key to delivering high-quality products on time and within budget.
Conclusion
In conclusion, a Bill of Materials management system plays an essential role in improving the efficiency of product manufacturing. It helps ensure that all materials, parts, and components are available when needed, reduces production delays, and optimizes cost management. By providing detailed information on the engineering and manufacturing processes, BOM systems enable manufacturers to deliver products that meet customer expectations while maintaining high standards of quality. A robust BOM system not only enhances performance and product quality but also contributes to the overall success of the manufacturing operation, providing significant value throughout the entire product lifecycle.
Source: Managing Efficiently Bill of Materials to Produce a Product